Revving into the Future: The Rise of the Electric Turbocharger
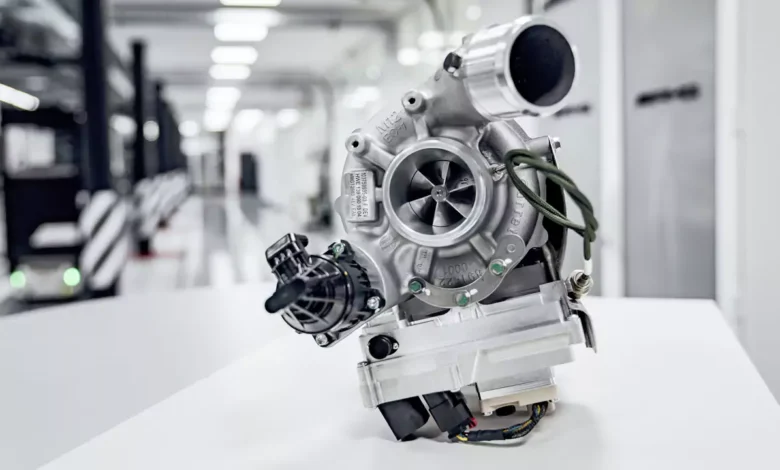
The image of a rally car speeding by at breakneck speed, accompanied by the growl of the internal combustion engine and the whistling of a spinning turbo, can send any auto enthusiast into a dopamine rush. But rally is rally, and we don’t live in that thrilling world every day.
In our quest to boost performance while reducing emissions and fuel consumption, cars now use forced induction, i.e., turbocharging the engine. Unlike rally cars, which need turbos to last just a few hours, our cars need them to last decades. Therefore, we can’t use the same methods as rally folks to keep our turbos at optimum boost all the time. So, we’re stuck with the downside of the turbo: the lag.
Throughout automotive history, turbochargers have seen significant development, resulting in various types with varying degrees of complexity. In this article, we’ll discuss the latest and most essential variety: the electric turbo (eTurbo), which addresses modern emission standards and the constant demand for more power from internal combustion engines.
A quick recap of turbocharger
If you’re reading this, you likely know how a turbocharger works. A quick recap: it’s a pair of turbines and compressors connected by a common shaft. The hot side is situated at the exhaust, where some energy is extracted from the exhaust fumes using the turbine. This turbine is coupled with a compressor on the intake side; as it rotates, it forces more air into the intake, providing more oxygen for a cleaner and more efficient burn of the fuel. This compression process generates heat, so the compressed air is passed through an intercooler.
The turbine’s spinning has its drawbacks. It requires a certain amount of force to get spinning, proportional to the turbine’s size. Smaller turbos need less force to spin and start rotating at lower RPMs, providing a boost at lower rev ranges and taking up less space. More giant turbines require more force to get spinning and generally provide a boost at higher RPMs. To overcome this, we use sequential turbos—a combination of both—or settle for a single-size turbo somewhere in the middle.
Electric turbocharger? What’s that?!
As the world tries to choke out the IC engine by implementing stricter emission standards, the good folks at Porsche made it their mission to keep it kicking as long as they can. A couple of years ago, they filed a patent for an electric turbo. According to the patent, they’ve managed to separate the cold and hot sides of the turbo, giving them more flexibility in terms of packaging, eliminating lag, and creating a more responsive turbo.
So how does it work? The concept remains the same, but instead of a conventional connecting shaft, an electric generator is used to virtually connect them. As the hot side spins, it generates electricity, stored in a battery, and used to spin up the cold side as needed, independent of the engine RPM at which the turbo would typically kick in. Thus eliminating the dreaded turbolag.
A few months ago, this translated into reality with the new Porsche 911. It now has more power with a slight weight gain and a bigger engine compared to its previous model by 0.6 litres. It uses only one turbo instead of twin turbos and runs at lambda equals to 1 throughout the rev range, even at cold temperatures. A reading of λ < 1 indicates air starvation (rich mixture), whereas λ > 1 indicates an excess of air (lean mixture).
Some might argue that this isn’t a proper ICE car but a hybrid. In my opinion, it’s the best hybrid possible, bringing F1 technology to the mass market. It’s not your typical hybrid like Toyota’s (which has its own merits in daily life). Electricity done right is the best thing for an ICE in this age of emission standards.
The new 911 uses a 2 kW battery pack to store recovered energy, turn the turbo as needed, and power the electric motor sandwiched between the engine and gearbox. The response benefit is vast; you no longer have to wait for exhaust pressure to build up a boost. Porsche says if you take both engines and put them at 2,000 RPM with the throttle closed, then open it, the old engine takes over 3 seconds to get to full boost, while the new engine reaches full boost in less than a second.
There is an electric motor sandwiched between the engine and gearbox, which feeds power directly into the 8-speed transmission, providing up to 110 lb-ft of additional torque right when you put your foot down, improving overall response. Depending on the situation, this motor draws power either directly from the generator of the turbo or from the stored energy, which is again charged up using the turbo.
Simplifying the process in five steps
- Maximum Power: The engine creates 478 horsepower at 6,500 RPM. The battery sends power to the electric motor, providing extra power to the transmission. The electric turbo recovers exhaust gas energy, sending it to the electric motor and finally to the wheels.
- Top Speed: To maintain top speed, the turbo recovers energy from the exhaust and constantly feeds the motor with electricity, providing an additional boost for the top end.
- Cold Starts: Floor the pedal during a cold start, and the engine runs rich. Excess fuel in the exhaust manifold can be burnt more effectively using forced induction from the almost instantaneous turbo and diverting a part of the air to the exhaust directly, raising the catalytic converter’s temperature and achieving lambda equals to 1.
- Boost Range: A larger turbo allows for better airflow and can be electrically spooled at a lower range to rapidly increase power, providing both low and top-end boost. This results in a higher and wider torque band.
- Lastly, we can use a bigger turbo instead of a smaller turbo, which only boosts the bottom to mid-range. Also, a smaller turbo is more restrictive and causes more cylinder heating, which in turn requires a rich fuel mixture to cool cylinder walls. In order to eliminate this, we can
use a larger turbo, which will let the exhaust pass quickly, and this can be spooled up using electricity at a lower RPM range to rapidly increase the torque and the maximum boost of the engine, where it will hold the turbine pressure on its own. Thus providing both low and top-end boosts.
The new Porsche 911 exemplifies this technology with a bigger engine and fewer turbochargers. The electrically spooled turbo reaches full boost in under a second, compared to the old model’s 3 seconds.
However, this technology is costly. But for Porsche customers, it’s all about performance and lap times. Over time, this technology can trickle down to upper mid-tier and mid-segment cars, benefiting a larger audience.
In conclusion, the electric turbocharger represents a significant advancement in automotive engineering, merging performance with environmental responsibility. While it comes at a cost, the benefits in terms of power delivery, efficiency, and reduced emissions make it a worthy investment for the future of internal combustion engines.